Shortcuts for Fixture Design
Fixtures are a necessary evil. Make designing them easier.
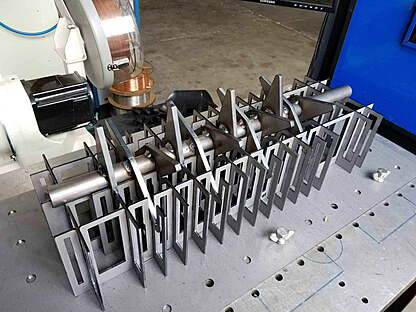
Welding fixtures can be expensive and complicated – and sometimes a product of simple luck and flaw. For manufacturers, the question is often “How fast can I get a fixture, at what cost and for what return?”. In this just-in-time (JIT) world, short runs are becoming common. So, when fixturing can be done in part or in total using a quick and cheap manufacturing process, bidding on such jobs becomes attractive. This is where technology comes in. Creatively inserting a little technology into your process can absolutely increase your efficiency.
Computer versus Traditional
For some time, software-derived fixturing has played a part in chip-cutting applications. Mainstream Solid-Based CAD systems have enabled tooling designers to use solid body subtraction to create a fixture model for any given manufacturing process. Depending on the component to be fixtured and the CAD system, this process can be quick and easy or not much better than a traditional, manual extrapolation using desired contact points, etc. Time to develop a fixture and the accuracy of the manufacturing are part of the efficiency equation, as is controlling material and conventional hard-tooling costs.
Adapting Existing Processes for Fixturing
Hard tooling for traditional fixtures often depends on costly milling and other “non-sheet metal” processes. So, how can this be minimized? The simple answer is to marry the processes and machinery you already have‒ lasers, waterjets, punch presses, etc. ‒ to the appropriate CAD system.
Smarter Welding
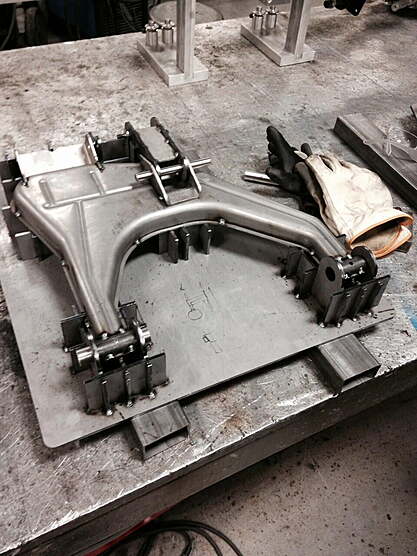
- Conduct a short run without a robot, using a precious manpower to do the welding and make or source an expensive fixture.
- Conduct a short run with a robot sitting idle while an expensive fixture is made or sourced.
Gearing Up for Repeatability or Upstream Changes
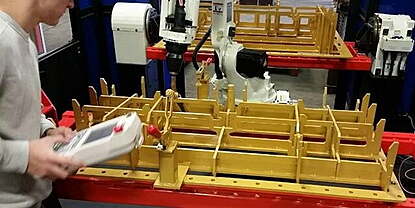
Automating Fixture Design and Assembly

Standardization, Reducing Storage Space

Staying Flexible for Simple or Complex Design
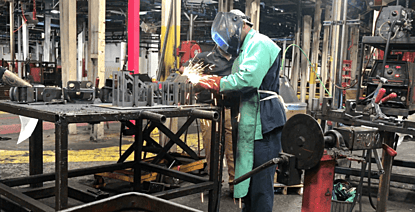
So, How Much Can Be Saved?
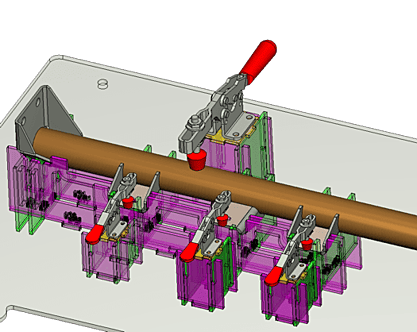
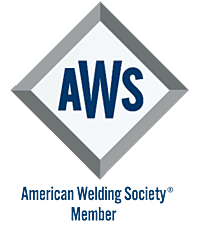